A micro 4 day project working with DIIP's 'Products for independent travel' brief.
Brief extract:
​
We challenge you to design an innovative product, primarily in plastic, that will provide a more comfortable and less stressful travel experience.
Your design should be:
-
Original
-
Sustainable
-
Cost effective to manufacture
-
Affordable and user friendly
-
Robust enough to withstand the challenges of any mode of travel
-
Meet the increasing demands of security checks
Given the highly competitive nature of this market, our judges will also be looking for a clear understanding of your product’s target market and how you plan to commercialise it.
​
There is a group of people who fly almost every other day for business. These people are exposed to health risks that are associated with frequent flying, such as deep vein thrombosis and cabin dehydration. Through extensive research, the issue of UVA exposure became a top contender.
Design In Innovation And Plastics

Insights into air travel health problems
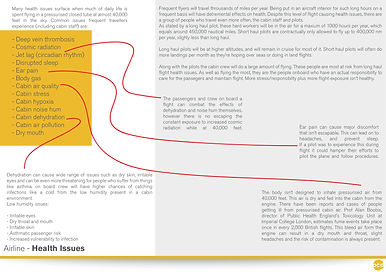

A micro 4 day project working with DIIP's 'Products for independent travel' brief.
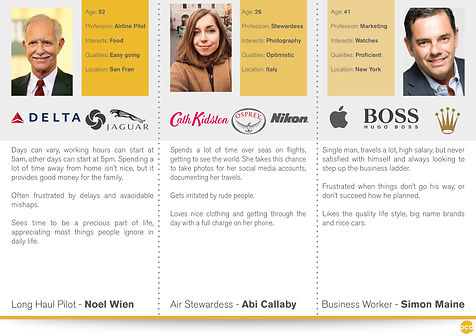
Contextual research
Gathering insights to the types of people who are in the frequent flyer class. User personas enables design choices to be made based on the target group. The chosen airline is Etihad for the long haul flights and the strong branding. The colours and geometric shapes could become an integral part of the design.
​
A quick look into the amenity kits given out on long haul flights sets the level of quality expected.
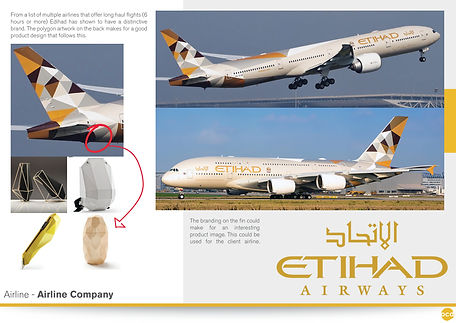
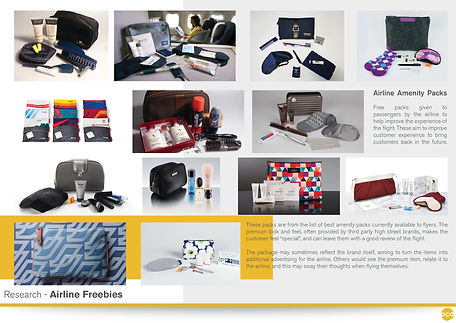
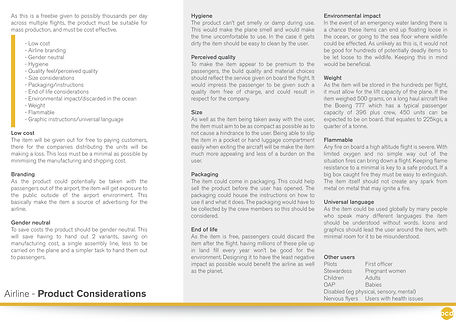

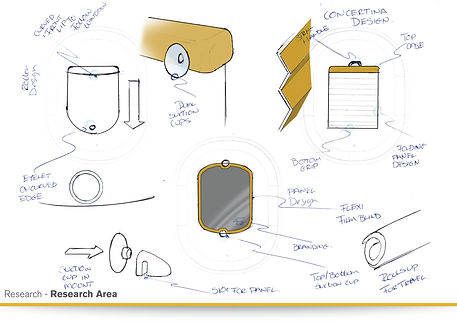
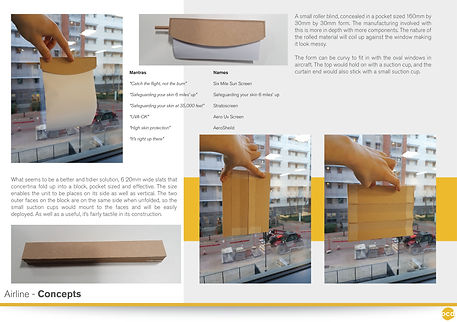
Concept development
The product considerations will set out goals for the end result, baring these factors in mind will keep the design process on the right path. Given the time scale of this project there was no time for expansive concept generation to explore every possibility, so keeping the concepts to a realistic standard was needed. The top 3 outlines were drafted up on paper and in sketch model form. Long haul aircraft window sizes were found, documented, and cadded up to set the products size limitations.


Final proposal
Moving away from the more complex polycentric hinge design for a simpler but less tactile design. The previous design had more foil segments, making more work for assembly, while reducing the effective area of UVA blocking foil. By making the foil take up the whole length of the product the users view of the sky was improved while minimising assembly stages. There are 7 components in total, duplicating parts through out for easy of assembly. The unit will fold up nicely, without damaging the foil. The overall size is roughly the same as a large chocolate bar, so packing it away after the flight isn't too difficult.

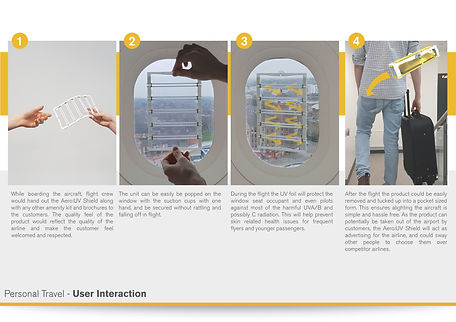
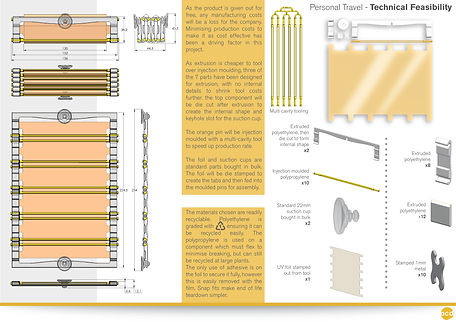
The finalising stages
Development on paper and Solidworks drove the project forward quickly, eliminating any issues found. The key to a successful product within this brief was manufacturability. As the item is a free give away it must be cheap to produce as each unit will make a loss on profit. Keeping component count down, while maintaining a quality look and feel expected, all within cost effective realms of manufacturing was the challenge.
​
Extrusion was superior over injection moulding for its cheaper tool cost. The profiles would be extruded, then die punched where needed for additional details.


For the full project log, click to open up the PDF.
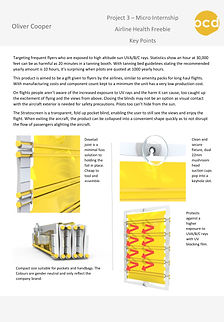
